Tech Report
Ribbon blenders are ideal for coating and mixing processes.
Technology Brief
Solid-solid mixing sometimes involves powders that need to be uniformly coated with smaller particles of a different component. The ingredient that is coated onto the bulk material is typically a very small percentage of the batch, thus requiring thorough and uniform blending. Ribbon blenders are proven to be highly effective for these coating and mixing operations.
Simultaneous coating and mixing
In certain industries, mixing of solid materials is required not only to blend different components but also to intimately coat a minor or trace ingredient onto the rest of the other particles in the batch. Examples of these minor components include additives such as flow aids, lubricants, pigments, preservatives or even active ingredients.
To maximize the functionality of the minor ingredient, individual particles of the bulk material have to be evenly coated. In many cases, inefficient mixing and coating lead to defects in the finished product.
Essential ribbon blender features and techniques
The batch ribbon blender is a standard workhorse used for solid-solid mixing. Its simplicity, functionality and affordability contribute to its widespread use in many industries. Agitator design varies slightly from one manufacturer to another but essentially consists of inner and outer helical ribbons which produce a well-balanced axial and radial flow of materials. Surfaces of the U-shaped trough are in close proximity to the agitator. High quality ribbon blenders are fabricated to achieve tightly controlled clearances in the range of 1/8" to 3/16". In coating operations, agitator-to-wall clearances are very critical especially due to the typically small particle size of the minor component to be coated.
Potential dead spots can be minimized by installing end plate scrapers and using a flush plug discharge valve. Interior surfaces must be well-polished and each weld should be ground smooth to prevent material buildup.
A useful technique in coating operations is to load the bulk materials first and the minor ingredient(s) last. In addition, optimal mixing in a ribbon blender requires enough batch material - a good rule of thumb is to fill the blender until product is sufficiently covering the agitator shaft. Working with smaller volumes, the blender can fail to generate adequate contact between the agitator and the product.
Gentler alternatives
When handling materials that are shear-sensitive, fragile or abrasive, cone screw vertical blenders and tumble blenders are sound alternatives to the more shear-intense ribbon blender. Talk to your blender manufacturer to explore your full range of options and ask abouttrial or rental programs to help in your equipment selection.
How ribbon blenders work
Ribbon blenders consist of a U-shaped horizontal trough and an agitator made up of inner and outer helical ribbons that are pitched to move material axially, in opposing directions, and also radially. This combination promotes fast and thorough blending. Tip speeds in the range of 300 feet/min are typical.
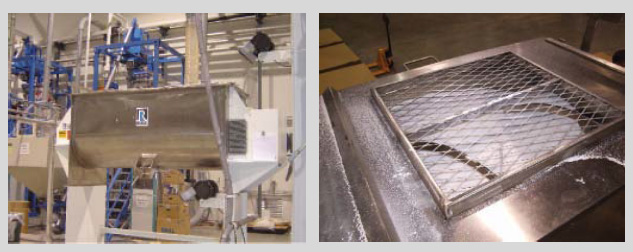
Ribbon Blender Installation Snapshots
Nova Chemicals Inc. develops and manufactures plastics and chemicals used in consumer, industrial, and packaging products. The company`s IMx technology has markedly improved the quality and insulation of expandable polystyrene (EPS) cups, sometimes referred to as "fat white cups" in the industry. Traditional EPS foam cups, which are 95% air and just 5% polystyrene, have a soft, bumpy surface. EPS cups made using IMx technology are sturdier, smoother and less "puffy", keeping liquids hot or cold longer. There is no need for a paper sleeve or "double cupping" to protect fingers from hot temperatures, thus reducing paper and plastic waste.
A crucial step in the manufacturing process is the uniform mixing of minuscule white polystyrene beads with a fine white powder lubricant, zinc stearate. If the lubricant isn`t evenly distributed on all beads, cups will stick in the mold or develop leaks when filled with a drink. Nova Chemicals relies on a 36-cu.ft. Ross Ribbon Blender to accomplish this step. After the 30-minute blending cycle, a quality check underthe microscope reveals consistent lubricant coating on each polystyrene bead.