Tech Report
Accelerate bulk powder dispersion into liquid.
Application Summary
An inline rotor/stator mixer equipped for powder induction is ideal for high speed mixing of bulk solids into liquid. Aside from high throughput, benefits include ease of operation, mobility and simple maintenance.
Solid-liquid mixing by the bulk
Mixing bulk solids into liquid can be challenging not only due to low solubility or resistance to wet-out/dispersion. The difficulty may simply be due to sheer volume. Certain processes call for exceptionally fast mixing of large quantities of powders such that the traditional method of adding solids from the top of an agitated tank is no longer efficient. In reality, any mixing step that normally takes hours using conventional batch mixing equipment can benefit from huge gains in productivity by shifting to a different system that can complete the batch in minutes.
High speed, high volume powder dispersion
One viable solution is the use of a specially modified rotor/stator mixer designed to generate a powerful vacuum within the mix chamber. The negative pressure produced by this type of mixer can serve to induct a wide variety of solids, from fine powders to friable pellets. In Ross mixers, this technology is called SLIM - Solids/Liquid Injection Manifold.
The inline rotor/stator SLIM mixer behaves like a centrifugal pumping device and can easily move liquid materials up to 10,000-20,000 cP. Dry solids enter from a separate port and encounter the incoming liquid stream right where materials are instantly subjected to high shear and turbulent mixing. The rotor turns at tip speeds ranging from 3,000 to 4,000 fpm and expels the mixture out of the chamber through the holes of the stationary stator.
The SLIM technology eliminates the clogging and poor dispersion quality associated with eductor-based systems. Operation is simple and the portable inline SLIM easily serves multiple process lines.
Typical induction rates
Below are typical induction rates for a 30HP inline SLIM model. Actual induction rates vary depending on powder flow characteristics, liquid viscosity, rotor speed, stator head, product temperature and restrictions in piping, etc. The rates shown here are based on powder induction into room temperature water at maximum rotor speed, inlet/outlet valves fully opened and using a large square stator head.
How the SLIM technology works
The illustration below shows how an inline SLIM mixer works. The liquid stream (1) enters the mixer and immediately encounters the powder addition. Drawn into the mixer by a powerful vacuum, the powder (2) is injected through the ported rotor directly into the high shear zone. The resulting dispersion (3) is expelled centrifugally through the stator openings at high velocity.
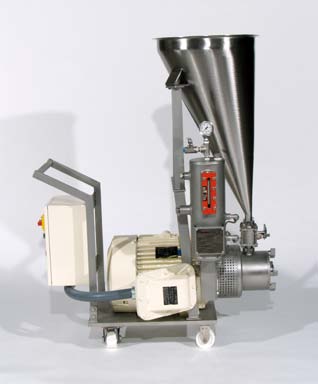
Sample Application: Asphalt-based Composite
A coatings manufacturer was looking to reduce the cycle time in their 6000-gallon batch where graphite powders were added and mixed into an asphalt emulsion using a large tank-mounted saw-tooth disperser. The inline SLIM proved to be highly successful in achieving a good immediate dispersion of the graphite and was able to reduce batch time from 3 hours to less than 1 hour.